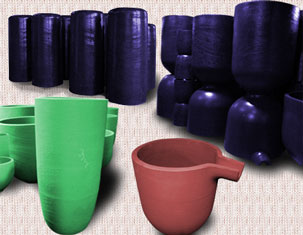
Instruction for Use
Requirements
Ⅰ. The preparatory work before the crucible installed. |
Ⅱ. Select suitable crucible base |
|
1. If the crucible furnace has residual internal slag, clear residue | 1. The crucible base and the bottom of the crucible should be the same shape, the crucible base size may be slightly larger the crucible bottom dimension size | |
2. Check to make sure crucible furnace wall and the bottom intact | 2. Crucible base should be inspected regularly and timely replacement of used crucible base | |
Ⅲ. Mounting and fixing of the crucible
|
Ⅳ. Preheating the crucible |
|
1. Installed between the wall and the furnace crucible should leave some space crucible swelling (8 - 12mm), use of wood, cardboard and other materials fixed crucible. Flame nozzle is not directly aligned with the bottom of the crucible | 1. First use empty crucible should be preheated crucible, the crucible 30 minutes preheated to about 200 ℃ and incubated 60 minutes to dry the crucible, the crucible sufficient to evaporate the moisture. | |
2. The support brick should be installed on both sides of the pouring nozzle for tilt furnace crucible with pouring nozzle, and to ensure that external forces free from the nozzle of crucible. Put into about 4mm cardboard or other materials between the crucible nozzle and the support brick as a pre-expansion space. | 2. After preheating the crucible continue to heat for two hours the crucible is heated to 900 - 1000 ℃, and incubated for 20 - 30 minutes, and then the crucible can be put to use | |
3. Crucible damp again or after a long time place to deal crucible warm up again before you can put into use. | ||
Ⅴ. Feed crucible
|
Ⅵ. Additives |
|
1. Non-ferrous materials in the crucible must be drying before adding. | 1. After complete dissolution of the metal material can be placed additives. Additives to avoid direct contact with the wall of the crucible resulting in premature failure of the crucible | |
2. Feeding metal material down should be gently, to avoid damage to the crucible overexert | 2. Excessive use of additives will shorten the life of the crucible, follow the additive instructions for proper operation. | |
3. Vertical metallic ingot and to maintain adequate expansion space reserved between the ingot and the crucible wall. Non-cross crucible when put the metal ingot in. | ||
4. You can also add some small metal materials into crucible first, as foreshadowing for bulk metallic materials. | ||
5. To speed up the molten metal, continuous melting can be retained in the crucible small amount of metal solution. | ||
Ⅶ. The use of crucible tongs |
Ⅷ. Product pouring |
|
1. According to crucible size, choose a suitable crucible tongs | 1. Cleaner, after degassing, should be cast as soon as possible | |
2. Crucible tongs to be sandwiched between a lower position in the crucible | 2. Use with spout crucible pouring, crucible should return to their original position after pouring rotation completed | |
3. It is not allowed to put the hot crucible on the cold surface of object when moving crucible, in order to avoid damage to the bottom of the crucible resulting scrap | 3. Crucible should be used to avoid prolonged for insulation work | |
Ⅸ. Empty crucible jobs |
Ⅹ. Clear the crucible slag |
|
1. Crucible need to temporarily stop using, should crucible metal solution emptied. | 1. Regular daily on the wall of the crucible slag cleanup operations, and to be cleared before the slag solidification | |
2. If the molten metal inside the crucible retained solidified, re-operation of the crucible is heated due to swelling of the crucible directly swelling bad to scrap. | 2. Slag removal operations to avoid scratching the crucible wall, causing premature failure of the crucible | |